3D printing, 3D printing tableware design
1. Using 3D printing system
In the early 1990s, Alessi designers began to use plastic materials to make prototypes during the conversion process from 2D design to 3D design to obtain three-dimensional complex parts that are closer to the design drawings to assist the introduction of new designs into production. With the increasing market demand for Alessi products, how to quickly and reliably obtain models for designers is a current issue.
Cristiano Colosio, CAD manager of Alessi, said, "We started using 3D printing equipment for offices at the end of 2004. At the beginning, we evaluated the equipment of various companies, but what impressed us the most was the ProJet SD3000 from 3D Systems. It not only has a good surface quality and is much more convenient than other equipment in post-processing.” Only good accuracy and material strength can do the assembly test.
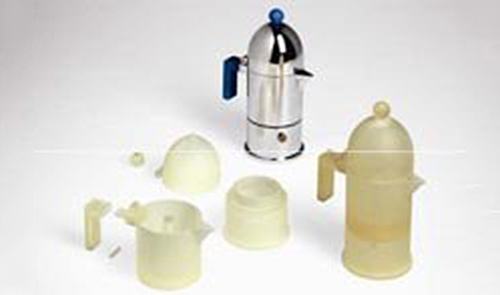
Alessi is looking for a 3D printer with low cost and low maintenance cost. The product is simple and easy to use and automatic work is of course necessary, and more importantly, it can be compatible with the existing office environment.
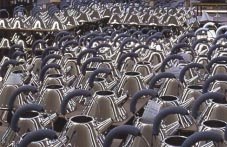
The ProJet SD3000 3D printer meets the above requirements. The model is made Not only the surface texture is good, features and details are also very good. During the nine months of purchasing the ProJet SD3000 3D printer, Alessi produced more than 600 models of various sizes, from small spoons to 150mm teapots. Until today, this model machine has been working for about 3000 hours, an average of 15-16 hours a day.
Model Manager Mauro Casalino said: "The ProJet SD3000 3D printer can fully meet our expectations, and the materials it uses are very good, and the models made have a longer life."
2. Redesign the "Cupola" product
At the beginning of 2005, Alessi decided to redesign one of their premium products-Cupola coffee machine, which has been loved by consumers everywhere for 15 years. The main purpose of this design improvement is to make the new product more in line with market demand. In the early stage of product design, we used ProJet SD3000 3D printer to make 6 prototypes of different designs. Many samples are used for assembly and functional testing. The assembly of components includes heating modules and other metal accessories. The models made by the ProJet SD3000 3D printer can even be dumped.
Colosio said: Knowing how coffee is poured from the spout is very interesting. During the test, we adjusted different parameters. It only took a few hours to get the newly designed 3D printed model. After we confirmed the prototype sample, we went to make the metal mold. The new La cupola model must retain the classic design of the past, and use rapid prototyping to make our work easier.
Using the ProJet SD3000 3D printer has reduced our model production costs by 70%, and can also make the communication between Aless designers in other countries smoother and increase productivity. Casalino said: The overall development time has been shortened. Each product only takes 5-6 weeks, which not only speeds up the process but also improves efficiency. Colosio said: Now we cannot do without the ProJet SD3000 3D printer, because it has given us unexpected gains.