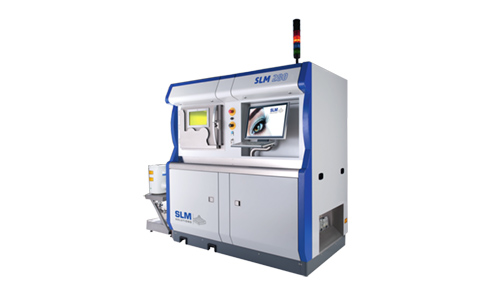
Tel:+86 135 7086 9158
PRODUCT LIST
|
1. Use IPG to produce water-cooled fiber lasers with a rated power of 700W (dual parallel lasers). In addition, SLM280 2.0 has a variety of lasers to choose from: 400W, 700W, 1000W can be freely combined, and it has a spot Adjustable function, 1000W+400W and 1000W+700W equipment have unique Hull-Core sintering process. 2. The digitally controlled electronic galvanometer adopts air-cooled mode, and a dynamic focusing lens is installed on the scanning galvanometer to transform the optical system into a three-dimensional scanning system. The dynamic focusing optical path system can ensure the spot size consistency in the forming area, and can change the spot size. The standard spot diameter is 80μm, which is the smallest in the same class and has a higher energy density. Different spot diameter lasers can be used for the same layer parts. Sintered in different areas. 3. The volume of the forming silo has reached the largest international equipment of the same level: 280×280×390mm, reaching 30,000 cubic centimeters, and the equipment of the same level: 250×250×325 to 20,000 cubic centimeters, an increase of 33% year-on-year! 4. Adopting the form of upper powder feeding, it can do the non-stop powder feeding work during the equipment processing. Using two-way powder spreading technology, the two-way powder spreading device is a key component to shorten the production time of individual manufacturing application parts, greatly improving production efficiency. After trial printing, the printing speed of titanium alloy is 4 times that of 400W single laser! 5. LCS is a detection and documentation system specially developed for SLM process. It can monitor the powder bed and monitor the unevenness of spreading powder. In the case of poor spreading quality, it can automatically spread powder or stop processing automatically. 6. SLM280 2.0 adopts the standard 2+1 multi-stage gas filtration solution, which increases the service life by more than two times, reduces the cost and greatly reduces the frequency of manual replacement. 7. MCS saves all printing process data, including molten pool monitoring, and performs real-time monitoring while the equipment is working. |
Copyright © Shenzhen Airboat Technology Co., Ltd. All rights reserved 【Backstage management】