Vauxhall Motors is a subsidiary of General Motors in the United Kingdom. During the production process, they need to continuously improve the quality of cars and increase production capacity to reduce production time and reduce costs.
In May 2014, the company began to introduce an improved engineering frame. Innovative variant models need to be processed, so a new part will be used to support the car body throughout the production process, making loading and unloading easier. This is a key component. It must be perfectly adapted to the machine to produce the correct clearance and to avoid damage to the car body during the production process.
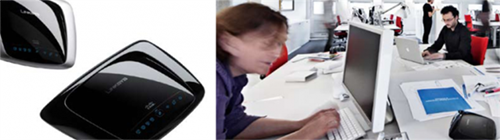
Graham Cooper is a senior planning engineer for the workshop conveyor system. He knows how critical these components are, and in order to produce smoothly, these components must be very precise. Since the final part is made of cast steel, the cost is high and it takes a long time to manufacture. He knew that if a small error occurred, the introduction of new equipment would be delayed by 6 months or more.
The team contacted Tim Warwick, the general manager of InfusionTech, a company that specializes in post-processing components to make them stronger, heat-resistant, and have other features that are not available on the original. Tim suggested using the ProJet 660 full-color printer and their liquid injection machine to make parts that can accurately and firmly support the entire car body during testing.
"The plaster material used in the 3D printing platform is not very strong in its original state," Tim mentioned, "but with our use of our tool materials, we can make very strong and durable parts that meet stringent requirements."
After receiving the 3D printed parts, Graham and Vauxhall's team installed them on the engineering rack and started testing. Grahma said that the performance of the parts is perfect, which can enable the whole team to achieve their goals: (As shown in the picture on the right: the 3D printed parts successfully supported the car body model during mechanical experiments)
? 3D printing allows us to check whether the position of the car body parts is in place before placing the order of the cast steel block, and whether it meets the accuracy of the CAD design.
? The printed block allows us to successfully modify the automatic loading station supporting the car body to prevent the car body from slipping on the engineering frame.
? Due to the use of printed blocks, when automatically loading one of the variant models, we found a problem with the height of a front positioning pin. So we lowered the height of the positioning pins and adjusted some aspects of the automatic loading station.
? The printed block allows us to modify the automatic loading station supporting the car body to prevent the car body from slipping on the engineering frame.
? This block allows our processing department to program the sealing robot for each variant model at the bottom of the car body.
When testing, it was discovered that the design needed to be modified to reduce the height of the positioning pins. Grahma and his team thought it was time to place an order to make cast steel blocks. These parts will cost tens of thousands of dollars and will take nearly 6 months to make. They have to make all the design data perfect.
"This process went well," he commented. "We need to test the parts, and we got the perfect solution through 3D printing."
Vauxhall’s team assessed that this process is very cost-effective, reduces design time and the time to apply these changes on the engineering framework, and reduces great risks.
“If we didn’t test these parts and made an order with the wrong design, it would cause 6 months of delay and a loss of 10,000 pounds. But because we use 3D printed parts, we can make sure that the design changes are It works perfectly, so that we can place an order for cast steel blocks."
In addition, he also said, “Being able to program the robot as early as possible in the process also brings us a huge advantage. This is not like the previous one until the steel block is found to be unqualified, which makes us delay more time. ."
"We will continue to use 3D printing and apply 3D printing to our design and engineering processes."