Toyota High Performance Development Corporation (HDP), founded in 1993, is a subsidiary of Toyota Motor Group in North America. Its main business is the development of high-performance racing car engines. HDP is the only engine provider for Indy Racing events and provides The prototype racing engine was used in the American Leman and European Leman endurance races.
In 2009, the company was developing the feasibility of using the touring car’s V6 engine for racing purposes. In 2010, the company developed the HR28TT engine (Honda Racing 2.8 liter twin-turbo), from engine design, development, testing, modification and practical use. For the event, because the development of the engine will freeze the entire event, basically they only have 11 months to develop the perfect engine, and the time is very limited.
Toyota has actually used the 3D printing system for the development of prototype samples and design modifications. However, they hoped that the progress could be more positive, so they purchased ProJet? 3000 CPX RealWax? Wax material 3D printer, using this brand new material to enable design It can be adjusted in real time, and the production of metal parts is much faster than traditional methods.
ProJet? 3000 CPX RealWax? It takes about two days to print out the complete engine, and then deliver it to the foundry for the manufacture of metal parts. The metal engine parts can be obtained in about 2 to 3 weeks. There are five parts of HR28TT produced in this way: left and right exhaust ducts, left and right rocker bodies and oil filter bodies.
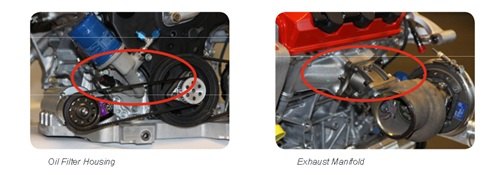
The final plan is to achieve the design task perfectly, and have an excellent performance in touring car racing. In terms of design, the traditional design and development methods and the 3D printer can save at least two weeks of development time. In terms of manufacturing, the main reason for the time saved is 3D printing wax raw materials, which can save the time of developing wax molds. The use of 3D printing to send the molds to the foundry reduces the original 8 weeks to 4 weeks. What's more important is that the development engine can be quickly modified to make the product nearly perfect.
Now HDP company has fully adopted ProJet? 3000 CPX RealWax? for all engine development work.