3D Systems (referred to as 3DS) and the European Space Agency (referred to as ESA) have cooperated to produce the injector, combustion chamber and combustion chamber for a two-component communication satellite engine through additive manufacturing technology direct metal printing (referred to as DMP). Expansion nozzle. These parts allow ESA to evaluate potential factors to further improve the current product design. In addition, direct metal printing experts from ESA and 3DS took advantage of the design opportunities of DMP direct metal printing to design and produce functionally separated alternatives for the above satellite engine parts. For example, the design of a monolithic combustion chamber can be combined with a thin-walled pressure Container and support for external structure. DMP direct metal printing can reduce weight, simplify assembly, produce fast and support later design adaptability. The cooperation with ESA is in line with 3DS's strategy: to provide its unique technology to support more superior space and aerospace manufacturing. For the space satellite engine, ESA further researches the direct metal printing parts of the additive manufacturing technology DMP.
Current status of DMP
Communication satellites are necessary for mobile Internet and guaranteeing commercial communications such as banking, television broadcasting, and weather forecasting. One of ESA's functions is to oversee the development of space satellite technology. As part of the internal funding project, ESA is studying metal additive manufacturing/direct metal printing, and they are evaluating its potential and future prospects for engine development.
As part of the research project, ESA chose 3DS company's direct metal printing, choosing 3DS because of their technical expertise and excellent customer service. 3DS has produced 3 key engine parts with current designs, as well as feasible DMP function design variables.
The injector on the satellite thruster combines the two propellants in a controllable manner so that they ignite spontaneously and continue to burn. The Venturi-shaped combustion chamber accelerates the emission of chemical gases and pushes the satellite into the correct orbit. The expansion nozzle affects the downstream airflow and then affects its motion characteristics.
Innovative fuel injector production
"DMP direct metal printing provides innovative replication to optimize the flow from the thruster valve to the combustion chamber," Simon Hyde said. Its design freedom allows ESA to reduce the number of injector assemblies to one, compared to more than 5 in traditional manufacturing. It also eliminates the potential risk of seal welding for hydraulic injection operations, which greatly reduces Cost and risk. By fully controlling the additive manufacturing process, 3DS's direct metal printing can obtain a uniform microstructure with a relative density of 99.98%. The number of metals and alloys, including titanium alloy parts, is gradually increasing.
DMP is also suitable for the thermally sensitive design of fuel injectors, which can prevent heat from tracing back to the sensitive propellant valve seat and the spacecraft itself. The fixture is no longer restricted so that the new design of the thermal element can control the conductivity by using a metal bracket. Built-in titanium alloy material suitable for flight (Ti6AI4V), the injector parts can meet the product guarantee requirements of the space section and rocket engine designers.
Separate combustion chamber function
The combustion chamber of a compact space satellite engine generally contains a convergent-expansion nozzle with an unsupported nozzle orifice. The propellant will complete the chemical reaction in the convergent part of the nozzle before the discharged airflow enters the expansion section through the convergent section. The existing separation chamber is designed to resist and launch, and the thick chamber wall transient load is linked to the non-operational load. Once everything is in place and operational, the combustion chamber no longer needs these thick walls.
Simon Hyde said that DMP direct metal printing allows the function of the combustion chamber to be separated under operational and non-operational loads. Intuitively, this translates into a support structure to support the thin combustion chamber wall and the welding flange of the expansion nozzle connection. The support structure made by 3DS's direct metal printing is a low-density grid, not a rough support. Because its bulk density is lower than 12%, the weight of the main combustion chamber produced by DMP is reduced or improved to the safety margin required by the structure.
Built-in Ti6Al4V material, this real wall material is a refractory alloy (for example: based on niobium, molybdenum, tantalum, tungsten and (or) rhenium) to withstand extreme heat of combustion. Further research shows that this innovative combustion chamber design involves the indirectivity of the grid in the stress field and its complex thermal shock. This grid will increase the effective surface emissivity, so it will affect the heat flux around the combustion chamber.
Large metal printing
ESA engineers also tested the use of DMP technology to make an expansion nozzle with an exit diameter of nearly 50 cm. This is probably the largest SLM part that has never been manufactured before. Speaking of the output of DMP, 3DS can manufacture any part geometry that can fit a box of 275 x 275 x 450 mm. The stress on the nozzle is relatively small and minimizes the cantilever mass. 3DS's direct metal printing uses titanium alloy (Ti6Al4V) to make the expansion nozzle, which largely meets the mechanical and thermal requirements of the expansion nozzle.
Hyde said that DMP offers different manufacturing advantages compared to traditional sheet spinning forming technology, which loses all design flexibility. DMP allows the engine's performance to conform to the customer's profile, even in the post-production process, there are many design choices.
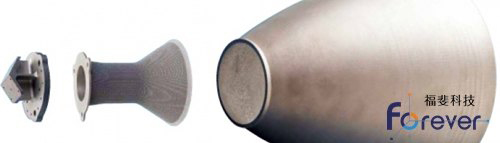