ProX™300 allows us to produce end-use parts faster and more economically than before. These parts are used in some of the harshest environments. -Gary Cosmer, CEO of Metal Technology
Since 1943, President Franklin D. Roosevelt announced that the U.S. Bureau of Mines had selected Albany, Oregon to study how to make titanium-zirconium alloys. These places have become hotbeds for the metallurgical industry. This decision provided the impetus for the booming alloy system to meet extreme needs.
Albany's Metal Technology (MTI) company is known for developing aerospace and defense applications. Its business includes the production of parts for the Trident missile project and various space exploration activities. MTI positions itself as an innovator in the global metal industry. Now, MTI is expanding the way metal parts are designed and manufactured.
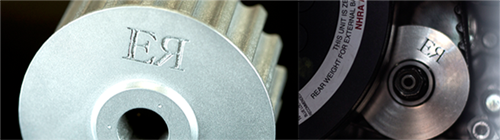
With the commitment to transform the manufacturing method of metal parts as the basic principle, MTI is already in additive manufacturing, using 3D Systems' ProX? 300 direct metal sintering (DMS) printer in production. ProX™300 uses a laser sintering process with a certain speed and complexity to manufacture pure chemical, completely dense and precise metal parts, which is unmatched by traditional manufacturing processes.
One of MTI's important strategies for using 3D Systems' ProX? 300 is to transfer rich metal manufacturing experience to new markets, industries and applications. So this year when the opportunity for motorsports as a perfect example of ProX™ 300 appeared, the whole team accepted it.
Gary Cosmer, the CEO of MTI and a enthusiast who spent a lot of his free time participating in this motorsport, soon realized that 3D printed parts would be very valuable in the motorsport market.
Cosmer said, "Before 3D printing metal parts, many times the cost of designing and producing one-time or small parts and components was expensive. 3D printing opened up a new way to think about the design of parts, printed parts Can have higher complexity and more functions, and have a lighter weight or better cooling inside the component.
In the neighboring state of Washington, English Racing needs to compete with the Mitsubishi 4G63 competition engine. The high-performance cars used by English Racing on the race track, especially the Mitsubishi Evo, are top-tier races of 1/2 mile. The vehicle travels more than 185 miles per hour and can exceed the speed of 10,000. The car’s factory oil pump drives the gear to increase the speed. Transformed into excessive oil pressure, followed by engine failure.
English Racing Company proposed an innovative way to solve this problem: They used a new gear with a large particle size to help reduce oil pressure. But making it is a huge challenge. The original gear is a casting. Generally, molds and tools are required to make a gear mold first, which requires a long customization cycle and expensive costs.
After trying to make this part for two years, English Racing has no hope of success. So at the beginning of 2014, the company discovered that MTI can quickly use 3D printing to prepare the design data of the part and use ProX? 300 to manufacture the part. The original part prototype only took 2 hours to print.
Within three days, this part was installed on a Mitsubishi Evo race car. The effect of this part is very good, reducing the oil pressure to a safe level and enabling the vehicle to reach the optimal speed.
"ProX? 300 allows us to manufacture end-use parts faster and more economically. These parts are used in the most demanding environments." Cosmer said. "By printing these parts, we can get the characteristics and design parameters of the parts, which are not available in traditional manufacturing. ProX? 300 also helps us to control the complexity, manufacturing speed and cost of the parts to the best, so that our customers can get better service.
After the parts were manufactured and tested, they used ProX? 300 across the country to manufacture 35 additional parts for different competition applications.
On June 27, 2014, the English Racing team used the newly-made oil pump gear in the Pikes Peak half-mile race, and achieved a speed of 184.0 mph, ranking first among the sedan-class vehicles. .
"This car runs great as we thought it was," said English Racing technician Zach Morgan. "We have run the vehicle through tests and we think we have a car that will win us. We don't know if we will always be number one. But our team is very excited."
"The application of ProX™300 is perfect for racing cars. We spent a total of 130 hours on this project, and the result is also very good." Cosmer. Zach Morgan said.
MTI can make a project from several years to only a short time, helping English Racing to save expensive costs and a lot of time.
"The entire metal industry is based on raw materials as a learning curve, and this idea needs to be changed," Cosmer said. "MTI is leading and driving the entire learning curve and is happy to promote the development of 3D metal printing. We don't think this is a trivial pursuit."
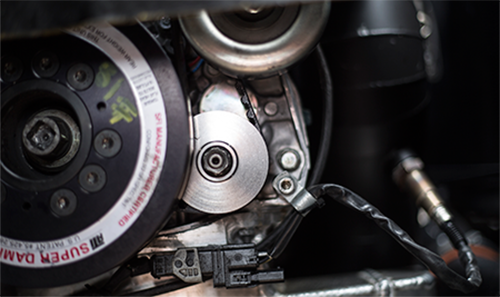