In 2013, Apple sold more than 170 million iPads worldwide. According to reports, there are 500 million iPhones, tens of thousands of Samsung Galaxy phones and various other phones being used, and this market is hot. Similarly, the demand for peripheral configurations, such as headphones, is very hot.
In the past 30 years, Fujigo is a highly acclaimed headset manufacturer. In the market, competition is getting fiercer and innovation is imminent. Fujiko, which started in Hong Kong, is no exception. They not only continue to explore better noise reduction functions, wireless networking capabilities and excellent sound quality, but also innovate more attractive products and pursue the fastest time to market. In order to gain a foothold in this market, these components are the core requirements of major competitors in the market.
In 2011, Fujigo had to take a step forward. They realized that in order to accelerate the speed of product development, their 200-person R&D team needed to adopt new practices and technologies. 3D printing is the first step in innovation. In June of the same year, the company manager asked a team to review, test and evaluate all major 3D printing technologies.
In the past 18 months, the team thoroughly tested multiple platforms according to its own needs: a fairly large build platform, high precision, neat and smooth surface of the finished product, and good material properties (to ensure that the parts can be columnar, drilled and screwed, It will not cause damage to the parts).
Only one 3D printer can meet these requirements: ProJet 7000. With the help of distributor Shanghai Meitang Electromechanical Technology Company, Fujigo introduced ProJet 7000. By May 2013, Fujico had installed the machine, trained the staff, and was set up and started to operate.
ProJet 7000 is the main SLA light curing 3D printer of 3D Systems. It can provide users with a high-precision universal size of 380 x 380 x 250 mm. Its two laser sizes enable users to quickly make parts while ensuring precise details, smooth surface and select layer thickness. The material VisiJet SL Flex tested by Fujiko provides excellent toughness for assembly testing, screw screwing and suitability testing, and has a perfect surface finish.
"Once we start, we will be able to see and appreciate the stability of ProJet 7000," said Mr. Wu Chunxiang. "This is perfect filmless manufacturing: we made precise samples of arbitrary and complex shapes, which was unimaginable before."
The R&D team is very excited to find that the ProJet 7000 prints overnight fast enough, which allows them to test the design performance of the product the next day.
"ProJet 7000 can immediately help our customers, our engineers" Mr. Wu said. "We have a new idea to evaluate product design, verify parts and assembly, perform sonic testing, review packaging design and reduce the risk of new product production tools in one day. In the past, the same process session fee A lot of time."
As part of the daily operation guarantee of ProJet 7000, Fujico sees various benefits. Preliminary evaluations show that in the total production and development time, a saving of 5% in the first year. Compared to the old 3D printers used by the team, it now saves at least 11% of materials. Most notably, the production speed of 3D parts is astonishing 62% faster than Fujiko's old technology.
"With the fiercely competitive market environment and increasing labor costs, we have to find better ways to help what we are doing now," Mr. Wu said. "ProJet 7000 allows us to meet the needs of the market and increase our competitiveness. We have completed product development very effectively, and we are also very happy to see that 3D Systems' 3D printing will improve our competitive advantage on our way forward." br>
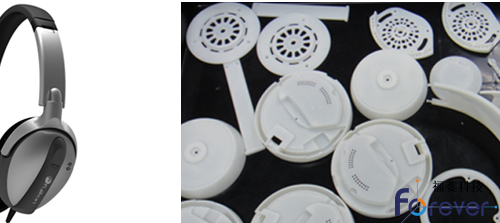