In February 2014, the American Precision Prototyping team, referred to as APP, faced a unique challenge: redesign, prototype, cast, decorate and ship 150 POWERADE? company hand baskets, these baskets are specifically for 2014 FIFA Propaganda equipment for competition preparation. They need to complete the entire work within 30 days. Using CAD, and SLA 3D printing, coupled with a flexible mind, the team completed the work early.
At the beginning of the project, the APP team got 2 early POWERADE® shopping basket designs and started working from it.
The first shopping basket is from the 2012 UEFA European Cup, and the second shopping basket is from the American League. For FIFA shopping baskets, the customer's goal is to combine the ergonomic design of the American shopping basket with the outline size and shape of the UEFA basket. The team must start designing the basket from the beginning.
In view of the tight schedule, APP company's program design stage is only one week. In this stage, the design of the basket still needs to be approved by POWERADE?. Company. There is another requirement for the design of the basket. The customer wants the final product to be divided into two, and the two sides can be connected together with a buckle to form a container that can hold 6 bottles. The team began to invest in this project, and they had an idea to meet the customer's requirements for size, but also meet the ergonomic and structural requirements. That is to say, two identical baskets can be used with 6 bottles, and the two baskets can be easily fixed together to become a whole basket.
In order to ensure that this idea is feasible, the APP team used 3D Systems' SLA technology to print a basket model that is twice as small as the actual one. This model is used to verify and check for omissions in the design. It took about 9 hours to print out the model of the basket and send it directly to the customer for review and confirmation.
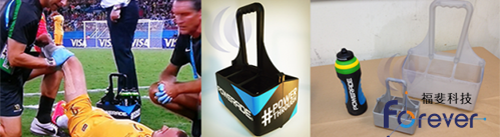
“We use the SLA stereo light curing process of the iPo 8000 printer to complete this design stage because of several reasons,” said Jason Dickman, director of APP company. “First of all, the accuracy of the parts produced by the stereo light curing process High, the error does not exceed 0.005 inches. Secondly, SLA technology has fast printing speed and high accuracy, which means that we can complete the preliminary model soon and get the verification and confirmation of the other company faster."
The sales executive of Coca-Cola Company looked at this model, which was twice as small as the entity, and requested some minor modifications. The team directly used the 3D CAD files to make changes directly. Then they started to use Accura60 resin material to make actual-size models, and it took about 15 hours to make 2 models per batch. These models will be used as a final check, and will also be used as a master mold for silicone molds and casting processes.
"We made 6 master molds in less than a day or two. The silicone molds were made for the later production stage of the shopping basket." Dickman mentioned, "It is impossible for us to use traditional processing methods to make this Changing the type of master model, 3D printing played a very important role in this project."
Molding and casting
Most plastic parts are made by injection molding. This process is to inject molten plastic into a metal mold of the desired shape. Because each part must be ready-made, the mold must be precisely machined. This is a time-consuming and complicated process. It is also very expensive, and it is impractical to produce it in a short time.
The APP company’s production team decided to use RTV silicone molds instead of injection molding. Silicone mold making is similar to traditional injection molds, but instead of using laboriously processed metal molds, they use flexible silicone molds to make parts. These molds are made very quickly, and have made very significant achievements in short-term product production. Because silicone tools are very flexible, they also take into account the undercut position in production and the structural problems that are more difficult than traditional injection molds.
Before making silicone tools, APP company prepared polished SLA resin master parts to obtain a finished product with a texture similar to injection molded parts.
Dickman said, "This allows us to imitate the appearance and texture of a mass-produced product without spending a lot of production time. It also helps us make a product that does not require additional coloring and processing. And it is strong enough to be able to Used throughout FIFA events."
For the parts themselves, the APP team used InnoTuf TP-4050 polyurethane material to imitate the texture of injection molded plastic parts. This material is provided by Innovative Polymers and is widely praised for its excellent impact resistance, flexural strength and ease of use. The final result is self-evident. The APP team and customers are very satisfied with the product, and it was produced under such a tight delivery time.
The APP team has produced 300 shopping baskets that are only half of them. If they are assembled, they can get 150 shopping baskets. Each tool needs to make 50 high-quality parts, which must look perfect and can be directly assembled together at any time.
Art and assembly
With half of the total 4 weeks left, the APP team started casting and assembling the 300 baskets.
"Because our initial SLA concept design is very accurate, the polyurethane parts we made only need a little post-processing, such as removing some small places such as vents." Dickman said, "After completion, these parts can be assembled at any time. Together, decorate, pack and ship out."
The APP team worked in shifts 24 hours a day and completed 40 to 50 castings every day. Finally, they entered the final stage to decorate the shopping basket. Each shopping basket will be decorated with a set of pre-designed vinyl stickers, printed on the stickers are the brand name of POWERADE? and the 2014 World Cup twitter special label. These shopping baskets will be held by the players in the Brazil World Cup, and people all over the world will see them.
Dickman said, "Without 3D Systems' fast and accurate 3D printing technology, it would be impossible to complete the shopping basket in such a tight time. We have completed an amazing project and the originality of our team is obvious to all."
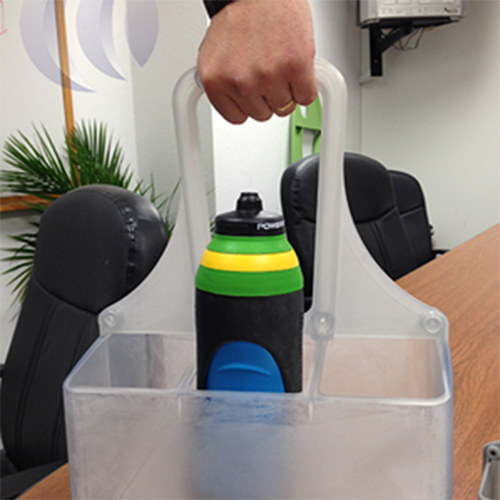