The news of 3D printing manufacturing prostheses to replace limbs is frequently reported. This is a wise choice. When combined with 3D scanning, the designer can make a special prosthesis according to the unique physical needs of each patient. Potomac Photonics is an expert in the field of micro-manufacturing, and their team found that using ProJet 3500 printers can get more unique 3D printed micro-implantable prostheses. In a recent case, they were asked to make a middle ear product with micro-elements to help develop a prosthesis for otosclerosis.
ProJet 3500 uses multi-nozzle printing technology to make durable high-quality plastic parts, and the layer accuracy reaches 32 microns. The simple and intelligent platform is extremely easy to use, and the choice of materials is very wide, including plastics similar to ABS; transparent color materials, blue and black materials; high strength, high flexibility and strong plastics. This is very helpful for high-precision models and parts of various types and sizes, including automobile manufacturing, aerospace and medical devices.
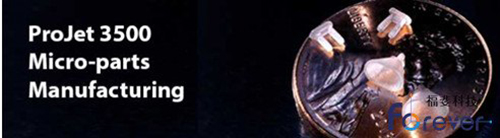
According to the American Academy of Otolaryngology-Head and Neck Surgery (AAO-HNS), hearing is a complicated process and dynamic in nature. The vibration of sound waves is transferred to the three tiny bones of the middle ear through the eardrum. This bone is usually called the stapes, and is used to help the inner ear fluid flow and start the hearing process. The NIH (National Institutes of Health) Institute on Deafness and Other Communication Disorders explained that otosclerosis is an abnormal hardening of human tissues. During lifelong reconstruction of new bone tissue, abnormal bone "remodeling" occasionally occurs. If abnormal bone remodeling occurs around the stapes, this bone remodeling will accumulate around the stapes, which will limit the vibration required for normal hearing.
AAO-HNS estimates that about 10% of white adults in the world are troubled by otosclerosis. NIH estimates that there are about 3 million cases in the United States. There is no medicine to treat, hearing aids can only be used for light patients, most people are diagnosed in their 20s, so this becomes a lifelong problem for them. Therefore, it is very important to try to develop solutions. Monika Kwacz is a researcher at the Society of Microparticles and Optoelectronics at Warsaw University of Technology in Poland. She is committed to researching small window stapes technology and leading her team to develop new stapes prostheses. "Intuitively," Monika explained: "It seems to me that 3D printing would be the best technology for making the first model. We need the first model for experimental verification to verify that the structure of the device is well designed. Yes. We can check the mechanical operation of this device. However, if we find that the structure of this device really needs to be modified, we only need to modify it in the CAD design stage, which is very simple.
Monika has tried another 3D printing but it cannot meet the stringent requirements of stapes design. Using 3D Systems' ProJet 3500 high-resolution 3D printer, Potomac Photonics can get a very miniature, precise structure and very small error value.
In view of the very small size of this part, once the design of this stapes is proven to be usable, the finished product of 3D printing may be feasible and very economical. At the same time, Potomac Photonics will continue to collaborate with Monika to produce miniature 3D printing solutions. It is no exaggeration to say that in the future, they may allow patients with otosclerosis to hear music again.