For the production of rolling shutters, we have more than 300 different models, and the fixed clamps must be perfectly adapted to the manufactured parts. Using the traditional grinding process, it will take a lot of time to match the curvature of the product. Using 3D printing, you can get the right shape and print out parts with very precise dimensions.
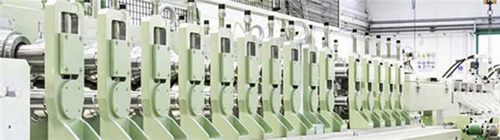
Customized solutions are already the mark of the manufacturer of Dallan S.p.A. This is a company established in Traviso, Italy in 1978. It mainly designs and manufactures a complete production assembly system based on roll forming and sheet metal processing in accordance with strict customer specifications.
"Our customers tell us what they want to produce", said Andrea Dallan, CEO and sales director of Dallan. "It can be a shutter or blinds, a suspended ceiling, gypsum board production or more. Then we develop an automated production system to manufacture this product."
In order to continue to diversify products and reduce time to market, the company has used a new 3D printing system on its traditional processing technology. Using the 3D printing of ProJet 3510, the company has enhanced its value proposition for customers to quickly customize parts.
Unique solution
For the production of rolling shutters, we have more than 300 different models, and the fixed clamps must be perfectly adapted to the manufactured parts. Using the traditional grinding process, it will take a lot of time to match the curvature of the product. Using 3D printing, you can get the right shape and print out parts with very precise dimensions.
Customized solutions are already the mark of the manufacturer of Dallan S.p.A. This is a company established in Traviso, Italy in 1978. It mainly designs and manufactures a complete production assembly system based on roll forming and sheet metal processing in accordance with strict customer specifications.
"Our customers tell us what they want to produce", said Andrea Dallan, CEO and sales director of Dallan. "It can be a shutter or blinds, a suspended ceiling, gypsum board production or more. Then we develop an automated production system to manufacture this product."
In order to continue to diversify products and reduce time to market, the company has used a new 3D printing system on its traditional processing technology. Using ProJet 3510's 3D printing, the company has enhanced its value proposition for customers to quickly customize parts.
Unique solution