In the knee-deep Liscomb bone bed in Alaska, there are numerous dinosaur bones distributed in the polar regions. Dr. Pat Druckenmiller can be very confident that he loves what he does. As the curator of the Earth Science Museum and associate professor of geology at the University of Alaska Faybank, Dr. Druckenmiller spent several months each year trekking the 3-foot-thick dinosaur bones of the Liscomb bed during his eight-year tenure. In the pile, these dinosaur bones are screened and classified. His uninterrupted work has advanced our understanding of prehistoric creatures that once lived on the earth, and even identified a new kind of dinosaur. This news was also reported by Acta Paleontologica Polonica.
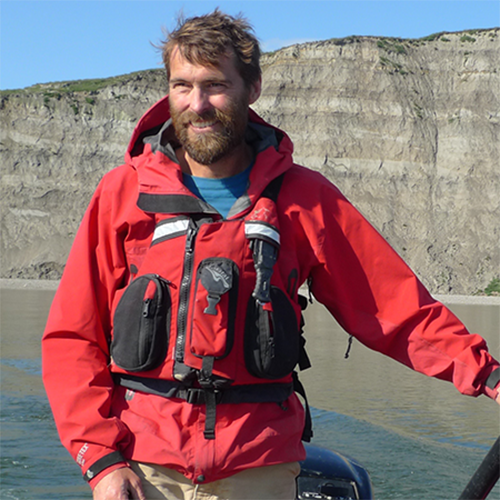
Sorting and classifying complex specimens in the field has a very high level of complexity. Druckenmiller believes that researchers now face a huge obstacle.
"In the Liscomb Bone Bed, there are thousands of dinosaur bones on the northern slopes of Alaska," he said. "Most bones seem to come from the same species of dinosaurs, but many bones are mixed together, and the joints are separated. This means that it is basically impossible to match whether this is the left bone or the right bone, the leg or the skull. I did it."
Facing the challenge of assembling a dinosaur skull, Dr. Druckenmiller asked Michael Holland for help. Michael Holland Productions is a creative content studio located in Bozeman, Montana, specializing in providing various services to museums and other educational and public service entities. Michael Holland is its principal. Over the years, Holland has used mathematical threads including 3D scanning and 3D printing to create exquisite exhibits for the museum. He immediately thought that he could use this method to deal with this project. Holland also asked Ian Sayers of Peak Solutions for support, a company located in Portland, Oregon, that specializes in providing 3D scanning and printing services to organizations and distributors.
"We can predict or creatively imagine what the skull should look like, but the bones we assembled may have serious asymmetry or distortion," Holland said. "The scientific method is to scan the complete fossil in 3D and then be able to Implement mirroring and copy them exactly. We can only do this through 3D scanning and 3D printing."
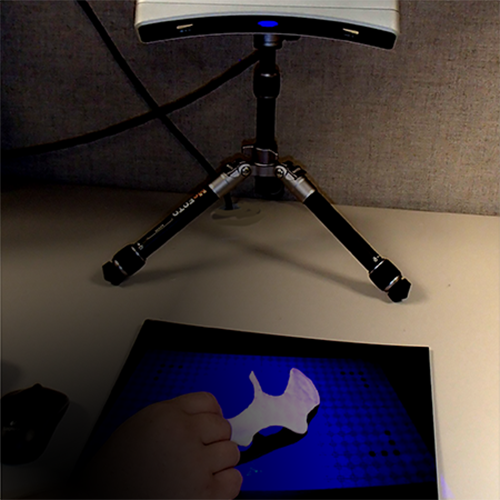
Sayers and Holland began to scan. They used plaster models of selected bones instead of the fossils themselves. Sayers used Geomagic Capture 3D scanner to work.
"The Jiemo Capture Scanner has helped us a lot. It just needs to be placed there to work properly—but it captured the most precise details of dinosaur fossils," Sayers said. "In a project like this, surface texture is very important, and 3D scanning and 3D printing is a perfect solution."
Sayers said the scanner took a few minutes to scan each dinosaur fossil, and in less than 5 minutes it created a complete 3D working model with each bone. Using Geomagic Wrap, the team members created accurate 3D data, and then used rapid mirroring to perform bone matching.
"Geomagic Wrap is great!" Sayser said. "It has the best tools and the interface is easy to operate. This software can work and create STL files almost at the touch of a button.
Within a day, the STL data of the mirror copy is ready and can be printed on the ProJet 660 full-color 3D printer at any time.
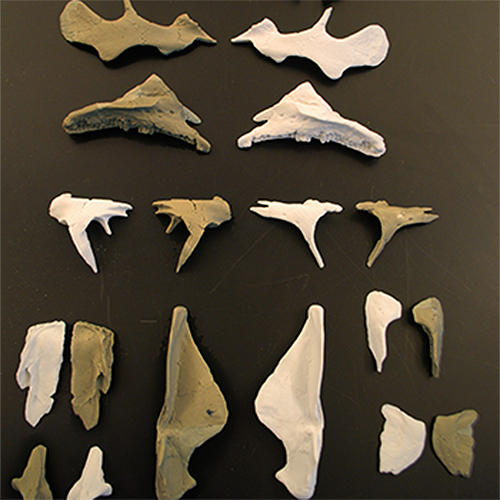
"ProJet 660 can make hard plaster parts, which is also an ideal surface material," Holland said. "We usually use the full-color function of the printer, but this time we use monochrome printing, so we can complete them. The parts printed by ProJet 660 are rigid and bone-like, and can be used with the glue we use to construct the skeleton. , Nails and nails are compatible, so this is a perfect choice."
Holland also said, "I also understand that it is very stressful to create 3 complete skeleton displays in a short time. 3D scanning and 3D printing have helped save a lot of time-I got 3D data almost overnight. And got the 3D printed material in one or two days.
Holland used matching plaster and 3D printed skeletal parts at the same time, and immediately put in his work to construct the entire dinosaur skeleton. Using some nails, threads and a lot of technical work, the entire team quickly constructed the entire dinosaur skeleton.
Druckenmiller said: "This is very cool. This is also an example of the innovation of 3D digital scanning and 3D printing in our professional field-this is not only for demonstration but also for the entire research. In short, we are confident that we can rebuild a new type of dinosaur skeleton. Demonstrate-this is much faster than we expected."