The development of science and technology has been promoting the transformation and innovation of manufacturing mode. From traditional manual manufacturing to automated processing, today's manufacturing under the wave of informatization is a new scene. As a new advanced manufacturing technology, 3D printing can meet the needs of market diversification and rapid manufacturing, and is becoming more and more favored by manufacturers.
According to a report by the consulting company Gartner, the global 3D printing market will grow at a rate of 32% in the next five years, and reach a market of 21.2 billion US dollars in 2020. 3D printing is widely used and can be used in medical, biological, education, aviation, consumer electronics, automotive and other fields. Although it currently accounts for less than 1% of the manufacturing field, the future development prospects cannot be underestimated.
To understand what 3D printing is, you can make associations from 2D printing. The difference is only the change from two-dimensional to three-dimensional (three-dimensional). That is, D printing has parameters for X-axis, y-axis, and z-axis, which is equivalent to two-dimensional The patterns are stacked one after another. And 3D printing materials are more diverse, from plastic to metal, etc. can be used on the printer to print three-dimensional models of different materials.
A new discovery or a new chapter in 3D printing
Recently, MIT researchers have developed a new method of spraying metal coating adhesion. This research may have a significant impact on metal 3D printing. Researchers used ultra-fast cameras to observe the spraying process and found ideal conditions for metal bonding. It is generally believed that melting is a good way to bond metals, but some researchers at the Massachusetts Institute of Technology recently made a research finding that cast doubt on some scientific views that were generally held in the past. Their findings may have a major impact on metal additive manufacturing.
This exciting research benefited from the high-tech imaging equipment used by the researchers: a high-speed camera using 16 independent charge-coupled device (CCD) imaging chips that can capture images in three nanoseconds. The optical kit was mainly developed by MIT postdoctoral fellow David Veysset, and its setting speed is so fast that it can perform tasks that were previously impossible to track individual particles ejected on the surface at supersonic speed.
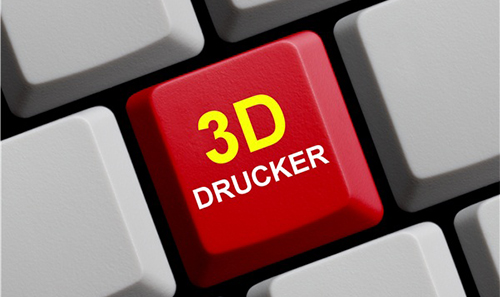
The camera can take up to 300 million frames per second, and this team uses this incredible technology to capture the painting process similar to a metal surface coating. The bonding effect is best when the jet impinging particles and the surface remain solid, but "splash" outward. Particles are not liquids, but like liquids. This "solid splash" is the best way to make metal particles adhere.
Since people have never been able to observe such a spray process correctly before, scientists have to estimate what happens when the particles hit the target surface based on the results rather than the process itself. Some people think that metal particles will melt when they hit the surface, while others think they won't.
As high-speed cameras are ready for more experiments, MIT researchers can now find a way to induce the correct conditions for this splash, which may lead to better metal 3D printing processes and improved metal coatings technology.
All-digital 3D printing business enters reality
Internet information technology is having a profound impact on traditional industries. The 3D printing company PROTIQ and the Berlin-based software company trinckle have studied in depth the process of 3D printing copper induction coils and developed a system from automatic ordering to on-demand production. The production process has achieved a fully automated and digital effect. Customers can configure the parameters online and order the copper induction coils they need.
The advantage of additive manufacturing is that it can be combined with an end-to-end digital process chain to reduce customer waiting time as effectively as possible. Users can simply select the basic shape they need and set application-specific parameters such as the number of turns, coil diameter, and the position of the connector itself.
Within a few minutes, the online configuration program can create a single 3D model, optimize the printing equipment, and then immediately produce the specified specifications. This means that manual CAD design that is time and cost intensive will be a thing of the past, and the time-consuming quotation preparation process will be eliminated due to the simple ordering process.
The traditional manufacturing process of manual bending and welding is time-consuming and costly. Therefore, it is not cheap to produce individually adapted inductors for each application field. In 3D printing, it can be manufactured by online configuration in a few simple steps. Heating coil. The follow-up production of 3D printing can be started as soon as the order is received, so that the finished inductor can be used within a few days. This combination of 3D printing and innovative e-commerce solutions accelerates the entire process from order creation to finished product delivery.