The Hankook-Tire design department uses 3D Systems' ProJet 660 3D printer as a key part of its conceptual design process. 3D printing technology can help design teams provide better communication between departments, save costs and improve the security of design data.
Founded in 1941, Hankook-Tire of South Korea is currently the world's seventh largest tire manufacturer and one of the fastest growing manufacturers. Now sold in 185 countries around the world, the company has developed a reputation for high-quality tires at reasonable prices. However, with the fierce competition from tire manufacturers, Hankook and Hankook adopted new designs and serious development of new products. As part of their commitment to provide first-class tires, Hankook looked for the best way to achieve rapid development and testing of innovative tire designs while keeping the secrets of design in development.
Lee said that "3D printing has become a part of his daily life." This is a very attractive technology that enables any idea in our hearts to be printed and gives it full color. With this idea in mind, the company invested in 3D systems Projet 660. The 3D printer uses ColorJet technology (CJP) to create a perfect full-color model that can be evaluated in form and function.
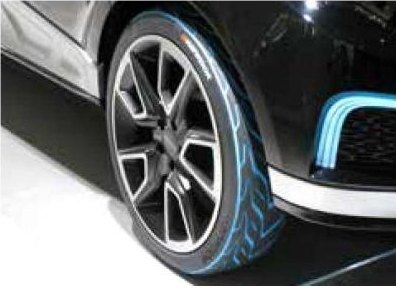
Myungjoong Lee, drawing in the Hankook Tire design department, used ProJet 660 to print the tire design before leaving get off work. When he went to work the next morning, this final model was already waiting for him. From the size of the created model to the finished sample, it took about seven to eight hours all night.
Lee said that "3D printing has become a part of his daily life." This is a very attractive technology that enables any idea in our hearts to be printed and gives it full color.
Lee found that 3D printing of ProJet 660 can reduce communication errors between design and engineering departments. Sometimes there will be friction between the two departments in the decision-making process.
Now, subtle and realistic 3D printing can be touched, inspected and observed, and there is a noticeable improvement in the process of communication and decision-making.
Meeting time has also been improved for this process, shortening by about 70% compared to before.
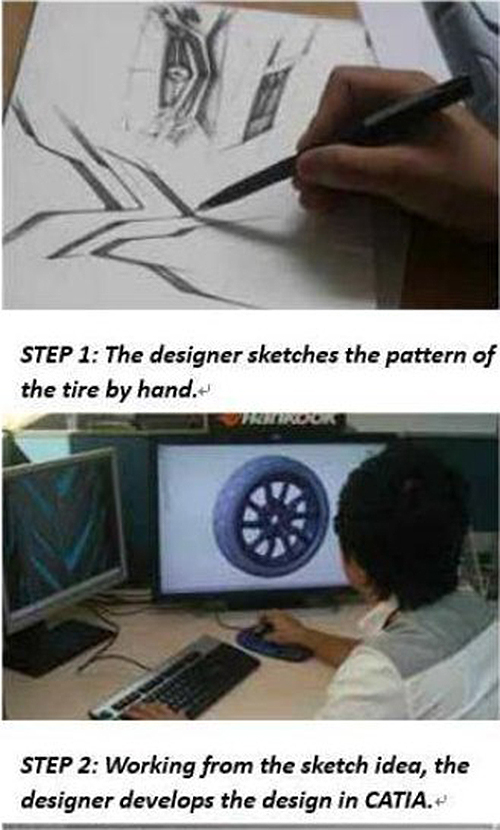
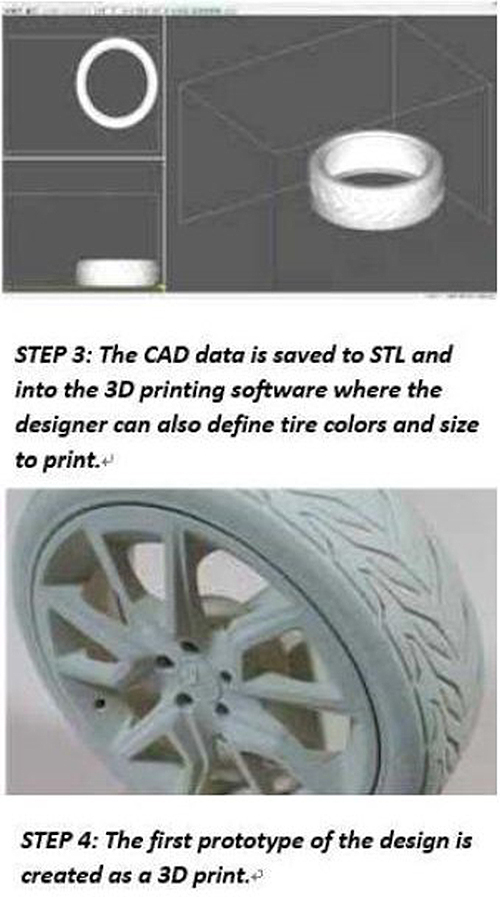
In addition, using ProJet 660 in the design process can save Hankook's money. Before using 3D printers, the design team needed to build physical models through external contractors. These physical models had to be made by hand and were very expensive. In addition, the design had to be simulated into various tire sizes. These hand-made models will not completely conform to the original CAD design.
Lee said "now", 3D printing obtains CAD data to create the correct size and perfect manufacturing presentation.
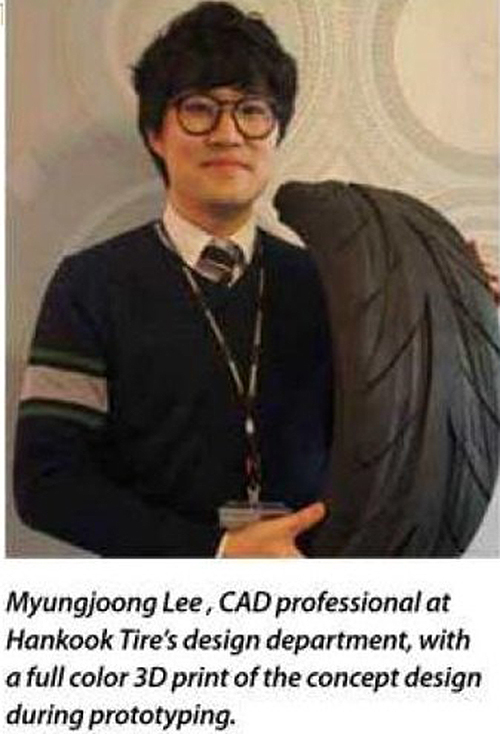
As a final benefit, the team can now be more confident that the innovative design seems to be safe to stay at home. With internal work processes, they no longer send confidential information to outsiders, thereby reducing the fear of theft and abuse of their intellectual property.